Otimizar o tempo de ciclo da operação impacta a produtividade da máquina-ferramenta
*Por Alfredo Ferrari | Foto: Shutterstock
O tempo do ciclo de trabalho na usinagem de peças é composto pela soma do tempo produtivo ou principal, em que ocorre o arranque de cavacos, e o tempo improdutivo ou secundário, como para alimentação da barra, carga e descarga de peças pré-formadas (blanks), troca de estação porta-ferramenta, medição em processo, entre outros.
O tempo produtivo pode ser otimizado através da aplicação de tornos cada vez mais avançados, da otimização dos parâmetros de corte (avanços e velocidades de corte), da aplicação de ferramentas de corte de alto rendimento compatíveis com o tipo de material, a operação a ser executada e a geometria da peça-obra, além da aplicação do fluido refrigerante ideal.
O tempo improdutivo, responsável por influenciar no resultado da produtividade de um equipamento de usinagem, vem tendo nos últimos tempos profundos desenvolvimentos, visando a sua redução e aumentando a eficiência de trabalho. Projetos mais avançados de máquinas-ferramenta, além de dispositivos e acessórios adicionais, que são agregados ao equipamento básico, resultam na redução dos tempos improdutivos.
Uma tarefa que afeta significativamente na produtividade de tornos automáticos, quer sejam aqueles acionados através de cames, como os digitais a comando numérico computadorizado (CNC), é a da carga e descarga de barras ou de blanks.
Magazine com troca automática de barras
Desde os primeiros tornos automáticos até os dias de hoje são aplicados alimentadores de barras, em geral com até 3,0 metros de comprimento e no máximo 80 mm de diâmetro, acionados hidraulicamente ou por pesos (gravidade), cuja troca de barra é realizada manualmente. É importante relatar que os avanços de barras acionados por pesos estão hoje reprovados por normas de segurança de trabalho em diversos países, inclusive o Brasil (NR-12).
Para aumentar a produtividade dos tornos automáticos horizontais de cabeçote fixo ou móvel, monofuso ou multifuso, foram desenvolvidos no início dos anos 60 os primeiros magazines automáticos de barras, que proporcionam as seguintes funções: guiar, alimentar e realizar a troca automática da barra. Tal desenvolvimento provocou um enorme aumento na produtividade das tornearias automáticas. Quanto mais comprida for a peça-obra e mais rápido for o tempo do ciclo de usinagem, maior será o ganho de produtividade do equipamento. Segue um exemplo do resultado na usinagem de uma peça, comparando-se a aplicação de um magazine com troca automática de barras com a de um alimentador de barras com troca manual:
- Tempo do ciclo de usinagem – 12 seg/peça
- Produção horária – 300 peças/hora
- Comprimento da peça mais a largura do bedame de corte – 150 mm
- Comprimento da barra – 3,0 metros
- Tempo de troca automática no magazine – aprox. 30 segundos
- Tempo de troca manual com alimentador – aprox. 4,0 minutos
- Aumento de produtividade – cerca de 80%
Além do mais, os magazines com troca automática de barras permitem trabalhar até três turnos sem supervisão, diminuindo os custos de produção e aumentando a rentabilidade da empresa.
Carga e descarga automática de blanks
Peças pré-formadas, como forjadas, sinterizadas e pedaços de barras cortados, podem ter um significativo aumento de produtividade pela aplicação do correto equipamento para realizar o carregamento da peça em bruto e a descarga da peça usinada. A escolha do equipamento ideal depende fundamentalmente do tamanho da peça-obra, de sua geometria e de seu peso. O ganho de produtividade depende de cada aplicação. Os principais equipamentos e suas características aplicativas são:
Magazines automáticos de alimentação – trata-se de projetos especiais de automatização, acionados geralmente através de componentes pneumáticos ou hidráulicos, e dedicados a trabalhos em uma única peça ou a uma família de peças homotéticas ou semelhantes. Em geral, aplicam-se na usinagem de peças de pequeno e médio porte em tornos automáticos a cames e a CNC e na produção de grandes séries.
Alimentadores cartesianos de pórtico (Gantry loader) – a peça é transportada pela parte superior da máquina, sendo a manipulação e troca das peças acabada e bruta feita através de garras, montadas em um mecanismo articulável. É um tipo de alimentador de peças aplicado em tornos CNC e muito recomendado para produzir, de forma flexível, peças tipo Eixo.
Robôs articulados – são posicionados na frente da máquina e é uma solução utilizada na produção de peças das mais diferentes formas e tamanhos em tornos CNC, de forma autônoma ou inseridos em células flexíveis de manufatura.
Conteúdo originalmente publicado no Canal de Conteúdo “A Voz da Indústria”. Republicação concedida pelo autor.
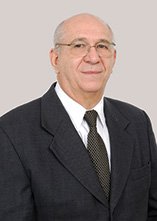
Alfredo Ferrari
Vice-presidente da Câmara Setorial de Máquinas-ferramenta e Sistemas Integrados de Manufatura da ABIMAQ