Como a fabricação baseada em nuvem melhora a qualidade na produção
*Por Francis Ritch, gerente global de usinagem digital da Sandvik Coromant, Suécia | Editado e traduzido por Vera Natale, editora OMU | Ilustrações Sandvik Coromant (Suécia)
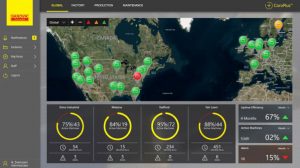
A manufatura em nuvem gera informações precisas e instantâneas de cada planta de produção, o que permite uma otimização contínua do processo
Já sabemos sobre a importância que o Big Data vem ganhando em diversos setores da indústria. Porém, por mais importante que seja estar atento a essa tendência de coletar dados, de nada adianta se não soubermos analisar esses dados e usá-los para repensar estratégias, processos e atitudes que podem certamente fazer a diferença nesse mundo globalizado e em estado “hiper conectado”. Mundo que materializa a cada instante cenas antes pinceladas só nos livros ou filmes de ficção científica.
Nesse artigo vamos tratar de elementos que a priori podem ser considerados coadjuvantes, mas que não são menos importantes. Devem receber igual atenção para a adoção de estratégias eficientes e bem alinhadas com as tendências da manufatura inteligente que se funda na conectividade. Estamos falando das soluções de fabricação baseadas em nuvem. Convido, assim, nossos leitores a começar a ligar os pontos para descobrir um pouco mais sobre a imagem que está se formando no horizonte de todos.
Para muitos, hoje ela pode ser nada mais que um tênue contorno, mas pode acreditar que ela formará cenários de contornos cada vez mais definidos. E de repente, você se perceberá não mero espectador, mas sim parte atuante dessa transformação digital, se é que já não está vivendo e participando de uma cena antes chamada de futurística e agora uma realidade mais do que tangível.
Vera Natale, editora
Durante muitos anos, apesar das recessões econômicas e dos ambientes de trabalho em constante mudança, o setor da manufatura continuou sendo um dos principais provedores de empregos e um expressivo gerador de receita em todo o mundo.
No entanto, embora muito tenha sido feito ao longo dos anos para garantir a qualidade dos componentes fabricados e aumentar a eficiência ao longo do processo de produção, ainda existem grandes fontes de desperdício que não foram tratadas de maneira efetiva.
O resultado final é que os níveis de despesas operacionais na área da manufatura ainda permanecem elevados. A Sandvik Coromant acredita que há oportunidades significativas para transformar esse cenário por meio de soluções digitais baseadas em nuvem.
É inegável que informação, conhecimento e dados desempenham um papel vital desde o planejamento de processos, passando pela usinagem até a avaliação da qualidade das peças. O pulo do gato, porém, é gerenciar esses elementos da forma mais precisa e abrangente possível, o que significa acesso e controle remoto a eles e, como consequência, otimização do processo de fabricação a tal ponto que as despesas possam ser significativamente reduzidas.
O gerenciamento de dados também possibilita analisar grandes volumes de diferentes tipos de informação com muita rapidez e fornecer feedback preciso sobre as características do processo de usinagem, permitindo aos fabricantes melhorar a precisão e a qualidade de cada componente que será produzido, por exemplo. Além disso, falhas de uma forma geral, incluindo erros de processo, podem ser eliminados de uma vez por todas. Isso significa que, uma vez que os fatores geradores de problemas são identificados e removidos do processo de fabricação, eles não ocorrem mais. Na verdade, o objetivo final é criar sistemas que possam constantemente se “auto-otimizar”, com pouca ou nenhuma programação/intervenção do operador, o que eleva o grau de eficiência da operação ou processo.
Desafios ainda existem
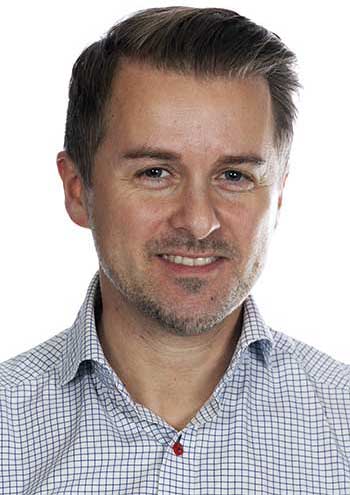
Francis Ritch: A Era 4.0 abre espaço para a tecnologia da informação & comunicação (TIC), combinada com o gerenciamento de dados baseado em nuvem
A realidade da grande maioria da indústria, porém, é outra. Uma das principais fontes de desperdícios na indústria metalomecânica é a falta de coleta e análise de dados qualificados da operação, o que impede a otimização do processo de produção. Além disso, máquinas individuais podem ter níveis de utilização inferiores a 50%, e somente cerca de 33% da energia que flui através de máquinas-ferramenta na fábrica é usada na fabricação efetiva das peças. Finalmente, apenas uma fração dos dados do processo disponível é gravada e ainda muito menos é analisada e utilizada para permitir previsões e melhorias.
É nítido que, hoje, o planejamento de processos sofre as consequências desse cenário. Isso inclui falta de uma sistemática de entrega contínua de dados do processo e falta de dados de feedback para um planejamento mais efetivo e que possa ter um impacto direto na qualidade e eficiência de todo o processo de fabricação. Ter garantia de qualidade de dados, informações e conhecimento é, sem dúvida, um grande desafio, mas não o único. Há uma preocupante falta de um modelo mais eficaz para transferência de conhecimento, o que dificulta o acesso à informação correta no momento certo. O resultado é um compartilhamento de conhecimento notadamente insatisfatório, assim como o nível de colaboração entre equipes envolvidas no processo de fabricação, onde quer que estejam localizadas.
Mudança de TI para TIC
Se o gerenciamento de dados, conhecimento e informações são a resposta para minimizar a ineficiência e maximizar a produtividade durante o processo de fabricação, é evidente que a tecnologia da informação (TI) já não é suficiente e deve haver um movimento consciente para a adoção de outras tecnologias, como a tecnologia da informação & comunicação (TIC), combinada com o gerenciamento de dados baseado em nuvem. Esse nível de transformação digital — que realmente oferece a promessa de coleta e compartilhamento inteligente de dados — é a garantia para que a fabricação “mais inteligente” se torne uma realidade. Reconfigurar a cadeia de valor dessa forma para que a baixa utilização da máquina seja algo do passado, é uma das principais funções de uma abordagem centrada em rede e apoiada por uma solução baseada em nuvem (TIC).
Para que a fábrica inteligente se torne verdadeiramente operacional, é essencial que a disponibilidade de recursos não seja com-prometida de nenhuma maneira. Para isso, os sistemas existentes de planejamento de recursos empresariais (ERP – Enterprise Resource Planning), sistemas de gerenciamento do ciclo de vida do produto (PLM – Product Life Cycle Management), os sistemas de execução da produção e outros tipos de sistemas de negócios operacionais devem ser totalmente integrados com todas as máquinas e todas as pessoas dentro da fábrica e de fora, se necessário. No momento, esse nível de integração total não acontece na proporção que deveria. Mas, com dados gerenciados por meio de uma entidade baseada em nuvem, finalmente será possível criar verdadeiras soluções de ponta a ponta, com garantia de precisão, consistência e conectividade. De seres humanos para seres humanos, humanos para máquinas e máquinas para máquinas. Em suma, as soluções de conectividade digital permitirão que as empresas melhorem todos os aspectos dos seus processos de produção, de ponta a ponta.
APIs abertas e sensores incorporados
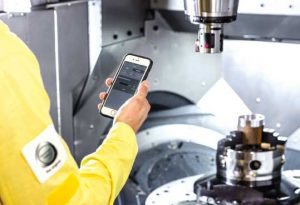
As tecnologias APIs (Interfaces de Programação de Aplicativos) abertas possibilitam que diferentes máquinas e sistemas interajam uns com os outros
Se o gerenciamento de dados, conhecimento e informações são a resposta para minimizar a ineficiência e maximizar a produtividade durante o processo de fabricação, é evidente que a tecnologia da informação (TI) já não é suficiente e deve haver um movimento consciente para a adoção de outras tecnologias, como a tecnologia da informação & comunicação (TIC), combinada com o gerenciamento de dados baseado em nuvem. Esse nível de transformação digital — que realmente oferece a promessa de coleta e compartilhamento inteligente de dados — é a garantia para que a fabricação “mais inteligente” se torne uma realidade. Reconfigurar a cadeia de valor dessa forma para que a baixa utilização da máquina seja algo do passado, é uma das principais funções de uma abordagem centrada em rede e apoiada por uma solução baseada em nuvem (TIC).
Para que a fábrica inteligente se torne verdadeiramente operacional, é essencial que a disponibilidade de recursos não seja com-prometida de nenhuma maneira. Para isso, os sistemas existentes de planejamento de recursos empresariais (ERP – Enterprise Resource Planning), sistemas de gerenciamento do ciclo de vida do produto (PLM – Product Life Cycle Management), os sistemas de execução da produção e outros tipos de sistemas de negócios operacionais devem ser totalmente integrados com todas as máquinas e todas as pessoas dentro da fábrica e de fora, se necessário. No momento, esse nível de integração total não acontece na proporção que deveria. Mas, com dados gerenciados por meio de uma entidade baseada em nuvem, finalmente será possível criar verdadeiras soluções de ponta a ponta, com garantia de precisão, consistência e conectividade. De seres humanos para seres humanos, humanos para máquinas e máquinas para máquinas. Em suma, as soluções de conectividade digital permitirão que as empresas melhorem todos os aspectos dos seus processos de produção, de ponta a ponta.
ICT integrado
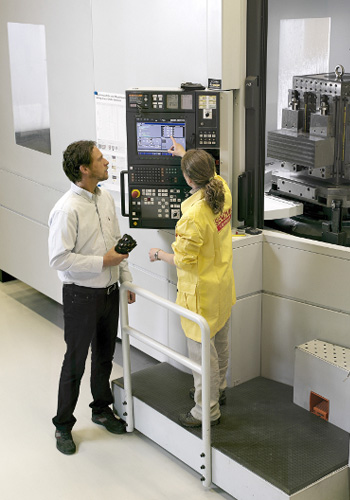
A integração de dados de pré e pós-usinagem resulta em máxima otimização e em todas as etapas da produção
Só com a implementação do ICT (Information and Communication Technology – Tecnologia da Informação e Comunicação) integrado do início ao fim da produção, é que os fabricantes podem obter uma cadeia de valor colaborativa, ativamente conectada em rede e em cada passo da jornada de fabricação. Em termos de logística de ativos, materiais e produtos, os fatores específicos que envolvem esse objetivo são rastreamento, gerenciamento e controle autônomo. Além disso, as configurações de fabricação do futuro precisam fornecer soluções personalizadas de produtos e processos que sejam igualmente eficientes, independentemente das variações de material e adaptações da máquina-ferramenta necessárias.
Outros fatores que influenciam positivamente a adoção de ambientes de fabricação integrados e baseados em nuvem abrangem modelagem virtual, diagnósticos preditivos, controle de qualidade autônomo, feedback e ajuste, diagnósticos, suporte remoto e aprendizagem efetiva de processos. Os benefícios e o efeito geral dessa abordagem totalmente integrada e de como a fabricação baseada em nuvem pode melhorar a qualidade do processo têm sido bem documentados.
Assim, enquanto o Big Data pode ser coletado e compartilhado em várias linhas de produção, ou mesmo em várias unidades fabris, é igualmente importante a capacidade de “detalhar” e ter acesso a informações precisas instantaneamente disponíveis em cada planta de produção — como a eficiência de uma única máquina, ou mesmo o desgaste de uma ferramenta individual. Por exemplo, a Sandvik Coromant desenvolveu uma plataforma que, com a combinação de várias fontes de dados e monitoramento do processo, permite análises abrangentes, melhorias contínuas e otimização. Isso ajuda a evitar forças de corte excessivas na ferramenta, falhas no rolamento do fuso devido a cargas excessivas, quebra de ferramentas. Também auxilia a controlar erros dimensionais e do perfil da peça por meio da deflexão estática da ferramenta, a aumentar sua vida útil em virtude da obtenção de um acabamento superficial uniforme e a construir, continuamente, o conhecimento necessário para uma maior otimização.
Conclusão
A indústria da manufatura em todo o mundo está evoluindo em sua abordagem e certamente se movimenta na direção certa. Os desafios são tão inevitáveis quanto possíveis de serem enfrentados no caminho rumo à fabricação baseada em nuvem. Sem dúvida, os ganhos são um maior grau de eficiência e efetividade, fruto da disciplina de abraçar de vez o monitoramento, a análise e o feedback dos processos, por meio dos recursos digitais disponíveis.
O resultado final do gerenciamento mais eficaz de informações, conhecimentos e dados, em todo o planejamento do processo, usinagem e avaliação de qualidade das peças, gera um processo de fabricação otimizado e que reduz as despesas operacionais. Além disso, os clientes se beneficiam com a entrega de produtos que eles sabem que são fabricados com uma precisão e eficiência de qualidade mundial. E essa garantia está se tornando cada vez mais valiosa em uma ampla gama de indústrias, entre elas, as do setor aeroespacial, extremamente exigente, em que qualidade, confiabilidade, rastreabilidade e velocidade de entrega são requisitos inegociáveis.
A digitalização via IIoT pode conectar processos de usinagem virtuais em tempo real de uma maneira nunca vista. Os limites entre as arenas real e virtual ficam cada vez menores.
A Internet Industrial das Coisas
A “Internet Industrial das Coisas” ou IIoT (Industrial Internet of Things) é a Internet das Coisas aplicada à indústria. Essencialmente, esse conceito abrange três áreas-chave que são essenciais em qualquer fábrica inteligente do futuro e que devem estar integradas — a computação de dispositivos, a computação da fábrica e a computação em nuvem.
A computação de dispositivos incorpora o processamento dos sinais digitais, interfaces de comunicação, conectividade do chão de fábrica, rede local, atualização e configuração remota, análise de hot data e interface com ferramentas e/ou máquinas. A computação da fábrica, por sua vez, inclui processamento dos sinais digitais, atualização e configuração remota, e também abrange análises de semi-hot data e interface com a nuvem. Finalmente, a computação em nuvem engloba a integração da nuvem para nuvem, monitoramento da fábrica, conectividade, segurança, e análise na pré e pós-usinagem.
Quero saber mais como ocorre. Há vídeos?